If you’ve landed here at Indigowares, you may already have an interest in living an environmentally friendly lifestyle. A huge part of this is putting consideration into how your clothing effects the earth. The best choice you can make when it comes to sustainable fashion is to select materials that come from the earth and can be returned to the earth, like natural fibres or organic dyes that are created through processes like harvesting indigo.
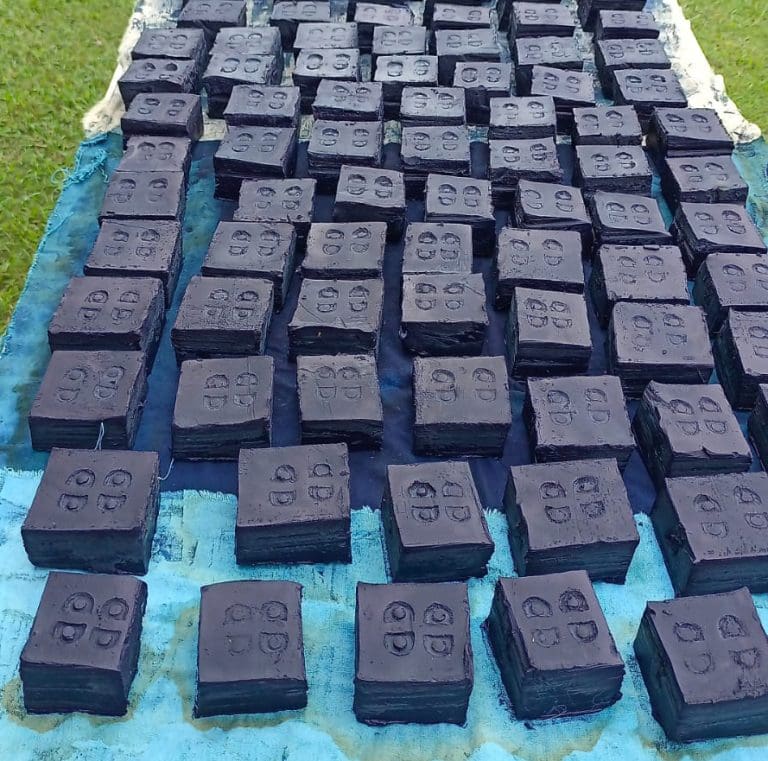
When you start thinking of how your clothes are made, all types of questions may emerge. Take indigo, for example. You may know that indigo is a natural dye, but where is indigo grown? How does indigo go from plant to a dye? What does an indigo plant look like? This is where we’re lucky to have someone like Kinny Sandhu, who supplies our indigo and shares so much about the process of harvesting indigo on her farm.
Kinny documented her most recent indigo harvest on her Instagram – you can click here to find her, or search for @kinnysandhu. Kinny has invited us to share some of her images here, so you can see a walkthrough of how indigo is grown, harvested, extracted…every step it takes before becoming the amazing blue dye that colours your clothing!
"Within a matter of days, we get to turn a lush-green crop into a blue dye and to be honest, it feels a bit like playing God."
A lot of the information we reference is from Kinny’s Instagram @kinnysandhu or @taraiblue, or at Kinny’s website at https://indigodesign.in/. Please check these out – we wouldn’t have this amazing and detailed account of where our indigo is harvested without her!

WHERE AND WHEN IS INDIGO HARVESTED?
Kinny and the people who work on her farm grow and harvest indigo in the plains below the Himalayas. This is in the Tarai region of Uttarakhand. The soil here is naturally rich; perennial and seasonal rivers run across the region. In preparation for growing indigofera tinctoria – the full name of the plant that produces indigo dye- the land is thoroughly ploughed, pulverised and weeded. We have an entire article on Kinny’s indigo farm and how she came to own it, which you can read here.
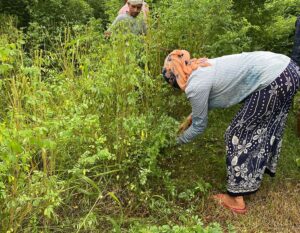

WHAT DOES AN INDIGO PLANT LOOK LIKE?
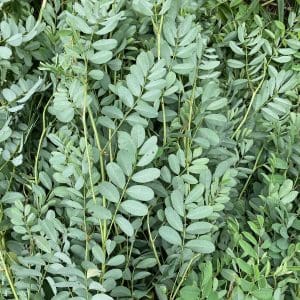
Kinny calls her crop Taraiblue, after the land it is grown on. She describes the process as entirely natural: “Tarai indigo is grown organically using natural compost on wetlands with ample sun and rain”.
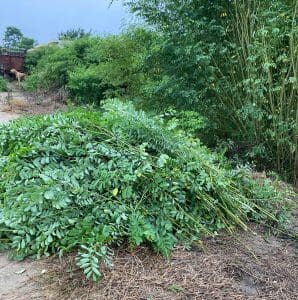
On Kinny’s farm, new indigo seeds are sewn by the beginning of March. The best time to harvest indigo is just before the flowers open, which is roughly three months later. Take a look below to see what an indigo plant looks like just before it flowers:
When fully grown, indigo stands at 7 to 8 feet tall, and is a dense shrub. The Tarai blue team of harvesters is made entirely of women. When harvesting indigo, the plant is cut to leave only 10 inches of the plant off the ground. Amazingly, this will regrow to full size in only a few weeks, when it will then be ready to harvest again.
Kinny shared the excitement of this process with us on instagram:
“Todays harvest! we have started on the large field and will be busy for a few days to get all of the crop in."

HOW IS INDIGO MADE INTO A DYE?
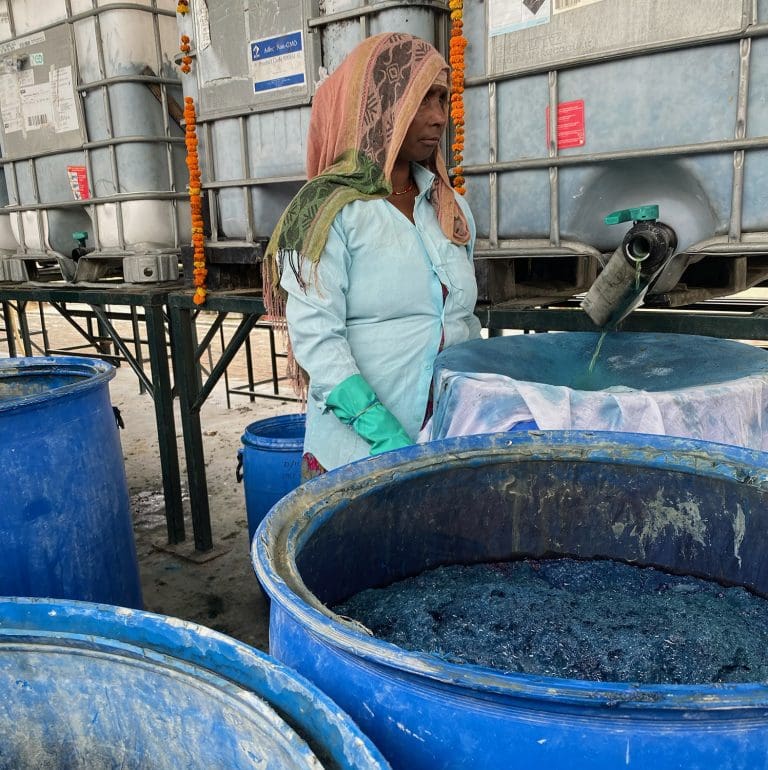
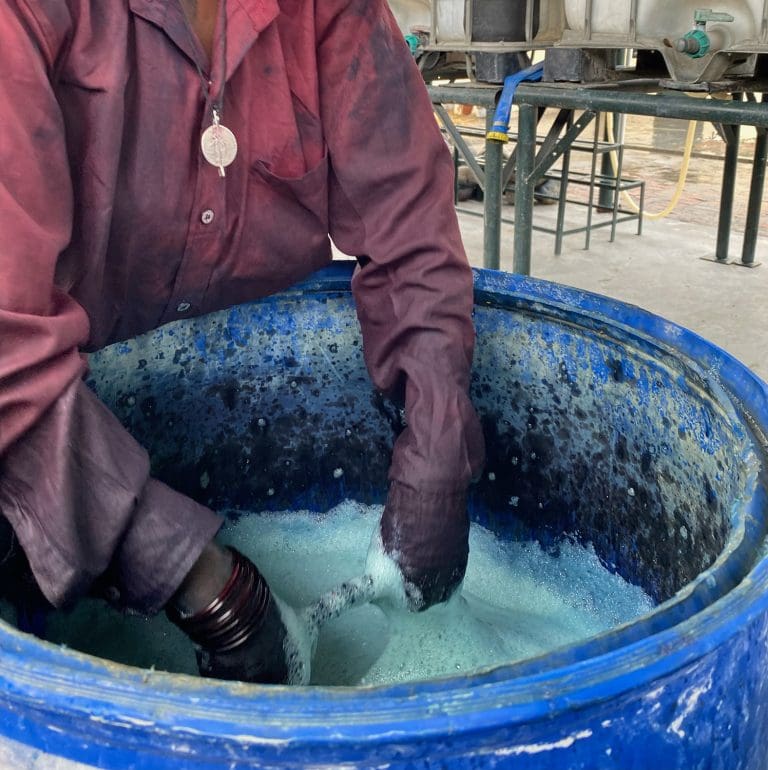
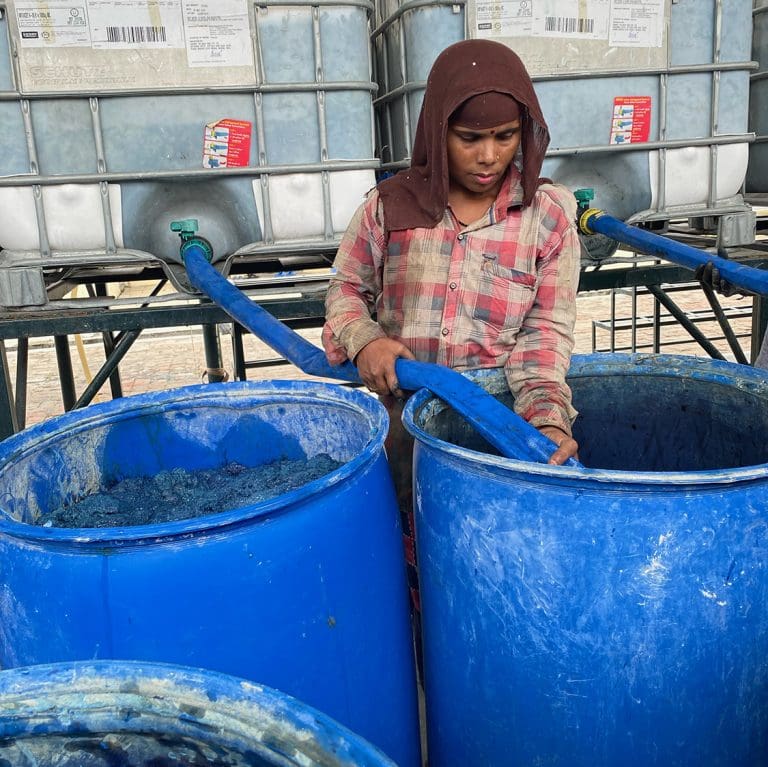
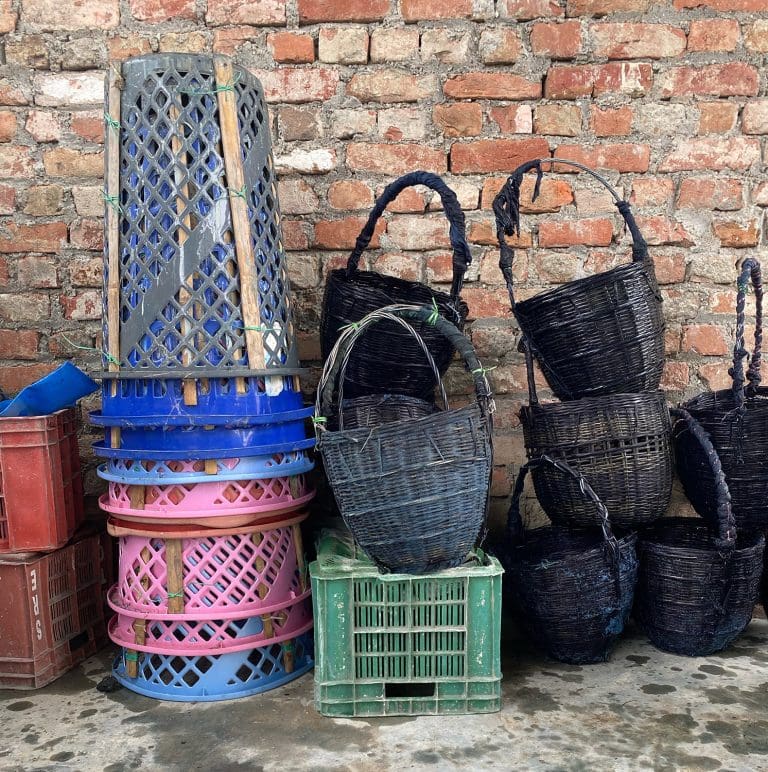
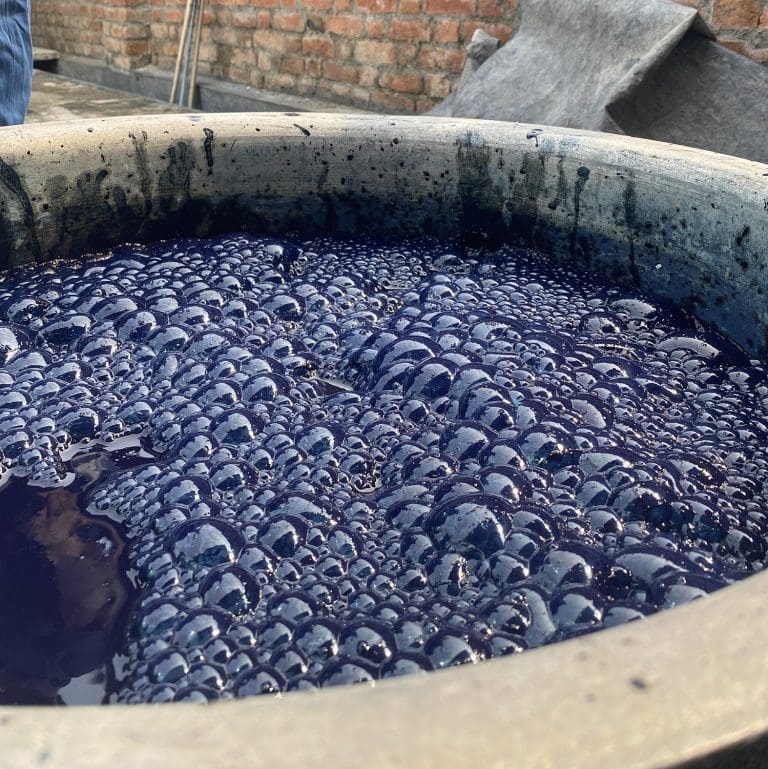
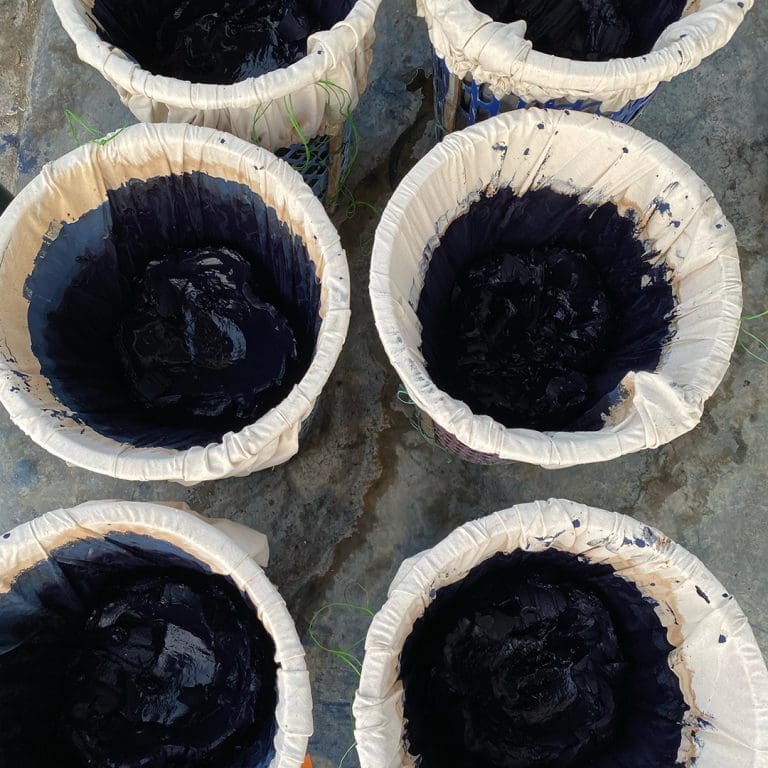
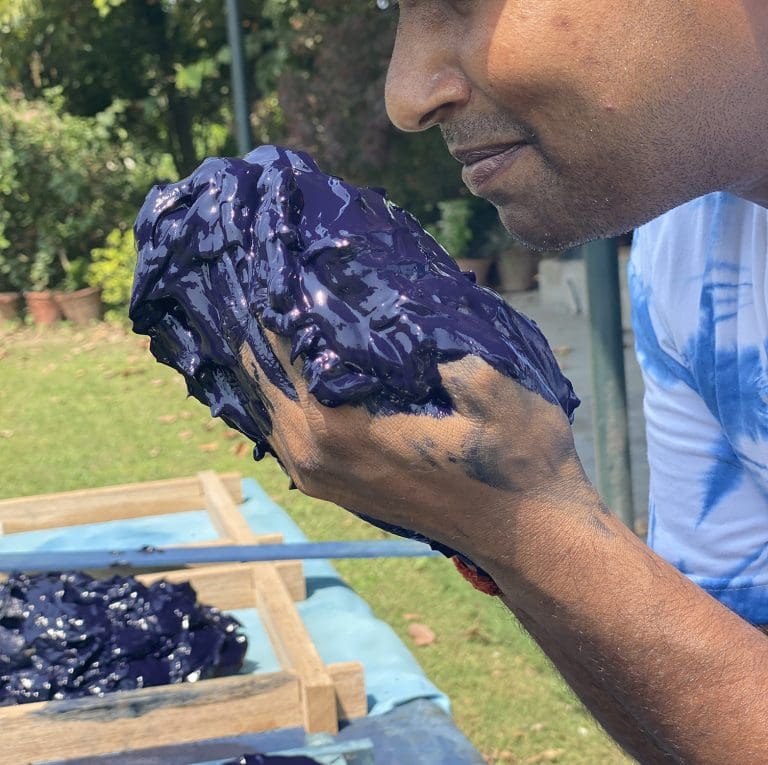
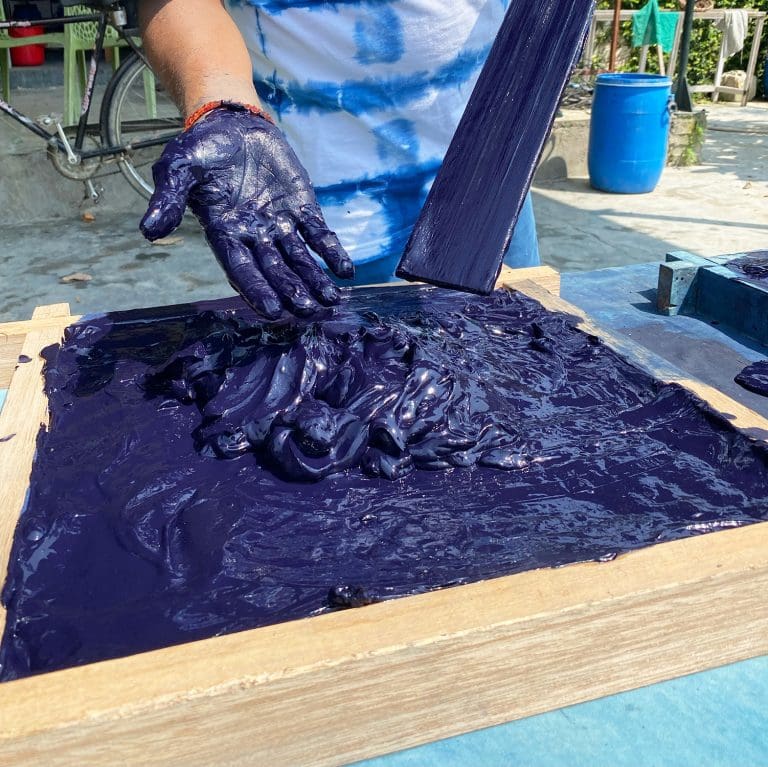
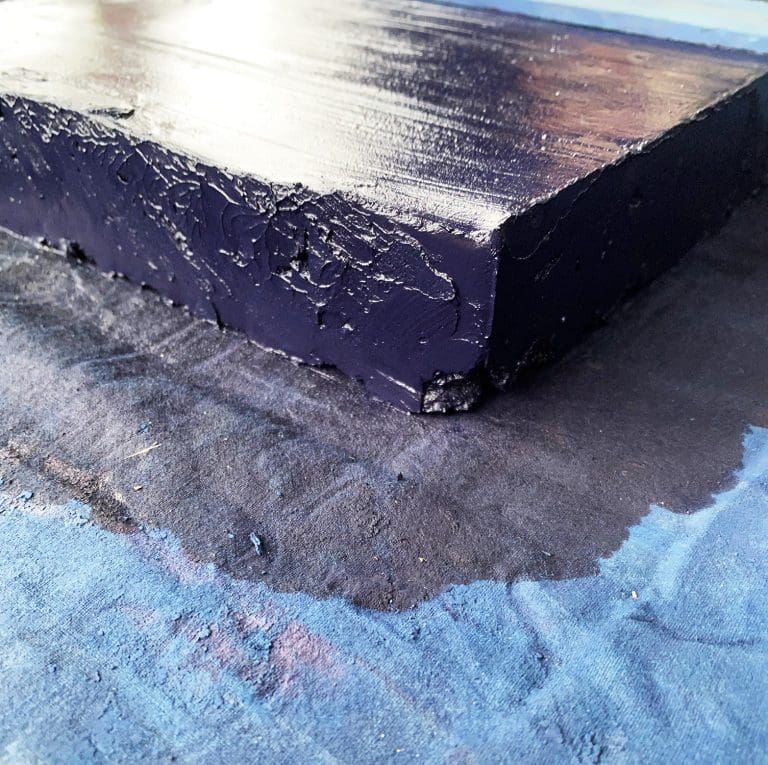
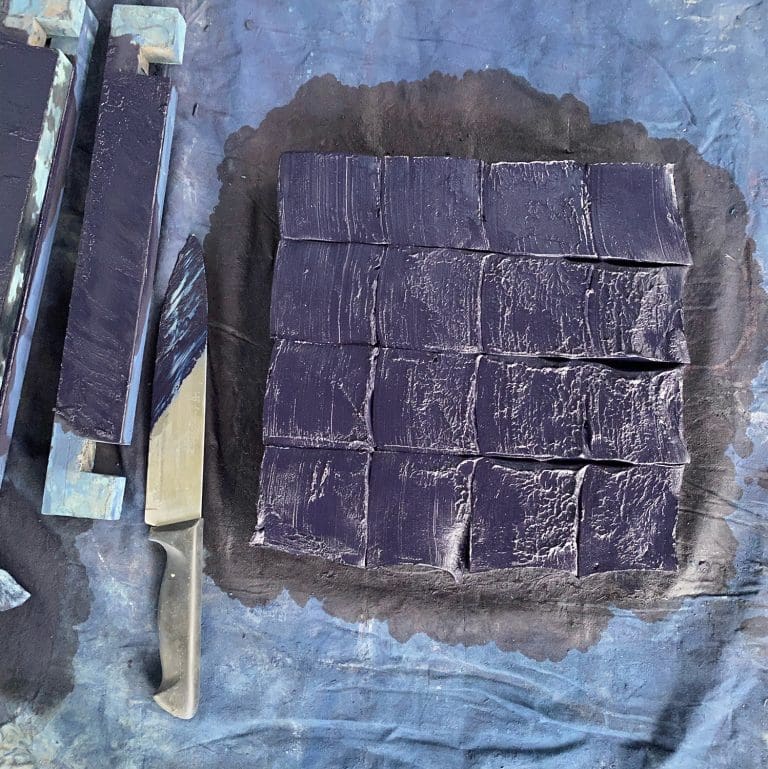
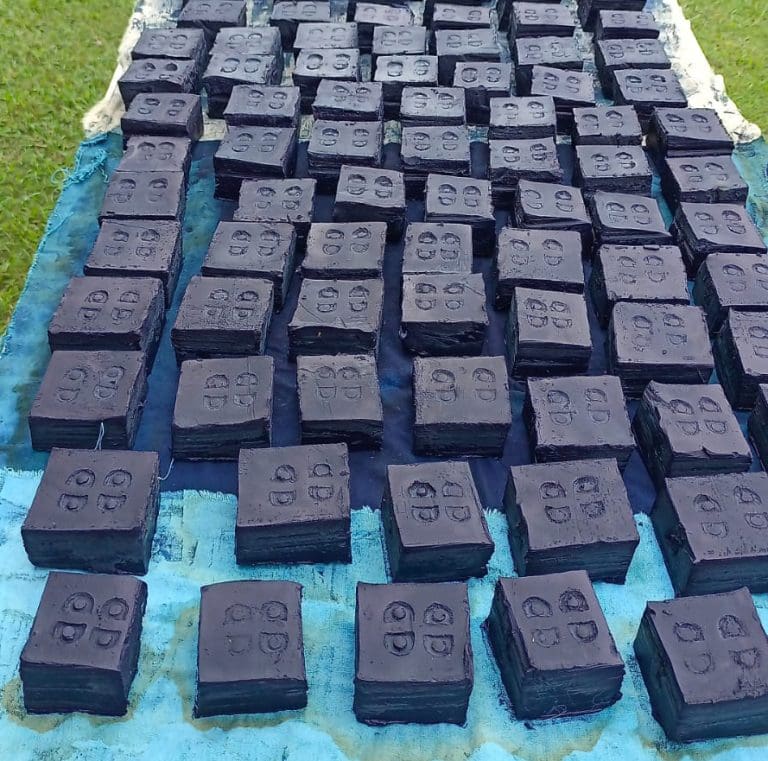
After the cut, the indigo is bundled and loaded into 1000 litre tanks, filled up with water. It is wet and weighted, and the fermentation process begins. When the indigo leaves are soaked, they release indican, which is the chemical precursor to indigo dye. It takes 12 to 14 hours of steeping for the indican to be hydrolysed/ broken down into indoxyl through chemical reaction with water.
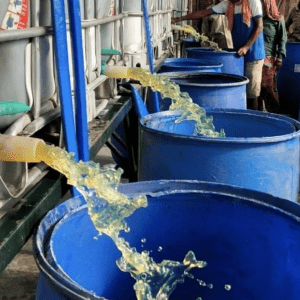
The leaves are then removed and returned to the soil via composting. What’s left behind is a yellow-green coloured water, which goes on to be processed even further. This solution is agitated in order to be oxidised, which creates a mass of indigotin that collects at the bottom of the tank.
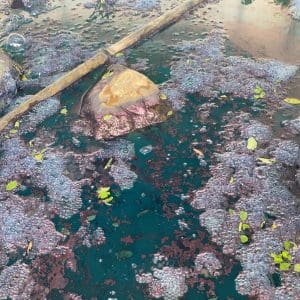
Kinny describes how she can tell if a crop is successful: “We keenly look for the blue bubbles and coppery shine on the surface of the tanks, a sign of a healthy crop.” The thick blue mass at the bottom of the tank is then passed through a fine cloth. This purifies it, then allows it to be sent on to be reduced down by simmering over a fire and then strained through cotton and allows to stand.
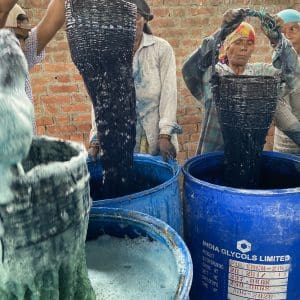
These are the exciting final steps that lead to the indigo paste that is then set in frames and allowed to dry in the Indian sun. Finally being sliced into cakes of roughly 100g in weight, as you would receive them if bought from Kinny or here at Indigowares, where we sell them separately or in our Natural Indigo Dye Kits.
-
Button Front Dress – Handloom Cotton – Natural Indigo
1 review -
Natural Indigo Dye Kit
5 reviews -
Sale!
Organic Indigo Plant Dye – Tarai Blue Indigo Cake
No reviews£32.40Original price was: £32.40.£21.60Current price is: £21.60. Add to cart

It’s been a true joy to watch the photos we’ve featured being published from Kinny’s farm. We’ll leave you with a beautiful caption from her, that perfectly describes seeing the indigo process all come together…
"When they say indigo extraction is a laborious process, we laugh it off. We don't think of the hours spent harvesting and crushing the leaves, the energy required to oxygenate the solution or the waiting for the pigment to strain properly. We only clasp onto the feeling of holding the thick indigo paste in our hands and marvelling at how it glistens under the sun. . After boiling the solution and straining it with a malmal cloth for 4 days, we finally, finally have our indigo paste and we cannot wait for tomorrow's big reveal! . How would you describe the feeling of finally holding something that you have been toiling over for a long time?"
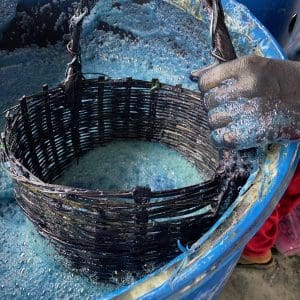
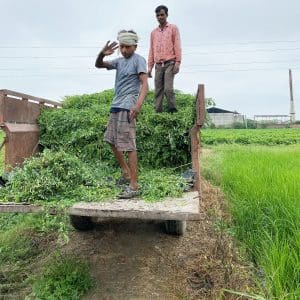
At the end of the day, the thing that’s most important to us is that we always keep in mind the circular process that goes into our naturally created garments. It’s important that we notice the details: Natural Indigo is a low maintenance crop, in comparison to something like cotton that takes up 20,000 liters of water to create just one kg.
By using natural dyes that are kind to the planet, like natural indigo, we are conscious of what we take from the earth. By dyeing and wearing natural fabrics, we are conscious of how our garments will be able to be returned to the earth. When we put all of this together, we are able to choose the processes that have the lowest impact, working with nature instead of against it.