Over the past year we’ve really built on our love of block printing here at Indigowares, coming up with timeless styles and patterns to bring this amazing craft into your life and wardrobe. There’s a good reason why we love this technique derived from Sanganer block printing: it celebrates hand craft, uses all natural dyes, and results in exquisite patterns on garments that will last for years to come.



It is artisan traditional craft like this that make our clothing far more than a trend, which is why I want to share the history of Sanganer, a region that’s been known for block printing and hand printed cotton fabric cloth for hundreds of years with you. Every time you wear a block print, you wear a little bit of Sanganer’s history!






The Origins of a Community
Long before Sanganer became a block printing mecca, it started as a small village on the bank of the Amanishah river. A collective of gardeners formed because of the fruitful land around the river’s edge. This is the beginning of the community that would define the colours and patterns that you’ll know as the very essence of block printing.


When designers create the patterns that you wear, the ideas don’t just emerge from thin air – everything has a history, and Sanganer Block Printing is a prime example. Block prints are founded on knowledge that has been passed on over the years, as members of communities like that in Sanganer learn the techniques within their families through observation and participation. This mean that your own wardrobe holds traces of this little collective of gardners gathering on the Amanishah river.






A Region Destined for Textile
Until the mid-1600s, Sanganer was known only for its natural dye and bleached cottons, and not yet known for Sanganer Block Printing. Then it reached a turning point; the town of Jaipur State became the artistic centre of the region, which is when the hand block printing community began to grow.
The setting was ideal, as the same riverbanks that gathered gardeners at the founding of Sanagner became the very spot for textile workers to dry cloth out in the sunshine. The water was perfect for processing dyes – to this day it is believed that water from the river adds special qualities to the cotton fabric! This intersection of location and craft boosted the town into a central hub for textile printing.
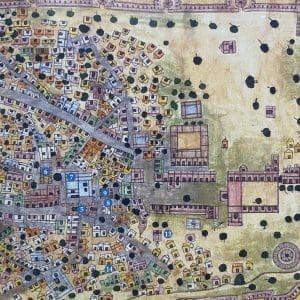
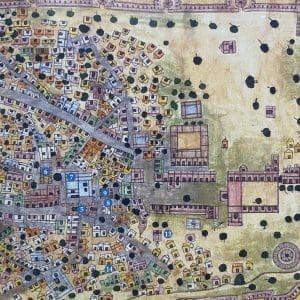






A Community Forms
As Jaipur became bustling, artisans from all over the country gathered in the region to share and inspire each other’s block printing process and knowledge. Groups formed within the community, like chhipas (printers), rangrez (dyers) and dhobi (washers). The Chhippa families were intrinsically linked to the block printing craft, their name directly lifted from the Gujarati word ‘chhapa’, meaning to print. They would bring their cloth bundles to Jaipur alongside dyers, bleachers and washers and return with the most beautiful block printed textiles and cloth.






The Traditional Sanganer Block Printing Process
Sanganer block printing practices have been passed through oral traditions over generations, which means that today’s Chhippas work in nearly the same way as they did years ago! Here’s an example of what this process looks like:


- First, cloth is scoured and bleached, soaked overnight in water mixed with components like sesame oil and soda ash. In the morning, the cloth is rinsed then dried in the sun. This process is repeated nightly for a week, and increases the fibres’ ability to hold dye during the hand block printing process.
- Once this week of soaking and rinsing is finished, the cloth in soaked a ‘harda’ solution – a dry powder from the fruit of the myrobalan tree mixed in water- until the fabric gains a yellow hue after drying out.
- Next, the process that we recognise as ‘block printing’ begins! Traditionally, black dye is used first on the light cloth, made from rust, unrefined sugar, gum from local trees and water, and the colour enters later in the process.
- This is the part that may feel most familiar, when the intricate patterns carved into wood blocks are painted with the dye and pressed repeatedly across the fabric. When the dye meets the harda treated cloth, the oxidisation creates a deep permanent black. Doing things in this order is similar to starting with an outline when drawing a picture.
- With this outline in place, a ‘begar’ is made: natural salt is ground and then mixed in a tree gum, with a pinch of geru added to create a luscious red ochre. The begar is then applied onto the design by the same process of wood block printing, and then the cloth is left to dry.




Once complete and washed of excess tree gum, the cloth is soaked again a copper dye basin known as a ‘tamda’. As the water in this basin is allowed to slowly heat it up, the raise in temperature causes the red dye to spread beautifully. This is an example of one of the most amazing parts of working with natural dyes – they react, change, and evolve into their beauty.
Washed in the river and dried, the white background (kharili zameen) that is traditional to Sanagner block prints goes through the one final procedure to bleach and brighten the printed design, and there you have it! All of the modern variations on block printing originate from these steps.






A Bigger Picture


Sanagner has been hugely important to India’s textile manufacturing industry, from the origins of craft through to more modern developments. Since the early 17th century, printers and dyers in the community of Sanagner have worked with biodegradable and eco-friendly dyes, making it central to environmental production.
There was a crossroads though, when the bohemian prints of the 1960s brought more diverse patterns like Sanganer Block Printing into style. This put a pressure on the craft that didn’t exist in its origins, driving more use of chemical dyes and screen printing. While a presence on catwalks and in the latest trends brought the aesthetic of traditional block printing into the western consciousness, it presented a challenge as the demands of fast fashion are never friendly towards environmental and craft-based methods.
On top of the statistics that say screen printers are outnumbering traditional block printers, there is also an increasing danger of a diminishing water supply in the rivers that are so vital to Sanganer’s block printing. The pollution of the clean mineral water that founded the Sanganer dyeing community is a huge threat to the industry and craft that needs it to survive.
Though mass production is always looming, Sanganer textiles maintain their tradition and legitimacy, even holding the Geographical Indication of Goods that means no mass produced copycat textiles made elsewhere can be sold under the name of ‘Sanagner Hand Block Prints’. The craft of hand block printing that started hundreds of years ago by the bank of the Amanishah river is still relevant and revered. That is why it is it is more important than ever to recognise, celebrate and wear traditionally and environmentally made block prints from regions like Sanganer.
All images and information referenced is taken from Sanganer Traditional Textiles – Contemporary Cloth, a beautiful book purchased at the Anokhi Museum of Hand Printing